Our Dictionary
Abbreviations used and standards observed:
EBG = extension spindles
TPE = Thermoplastische Elastomere
PE = Polyethylen
DVGW GW 336-1 (A)
- Technical rule – Code of practice DVGW GW 336-1 (A) │ September 2010 Buried fittings – Part 1: Standardisation of interfaces between gate valves und extension spindles
DVGW GW 336-2 (P)
- Technical test specification DVGW GW 336-2 (P) │ September 2010 Earth installation sets – Part 2: Requirements and tests
DVGW W 336 (P)
- Technical test specification DVGW W 336 (P) │ October 2013 Water tapping valves; requirements and tests
DVGW W 363 (P)
- Technical test specification DVGW W 363 (P) │ June 2010 Shut-off valves, backflow preventers, aeration/deaeration valves and control valves made of metallic materials for drinking water supply systems – Requirements and tests
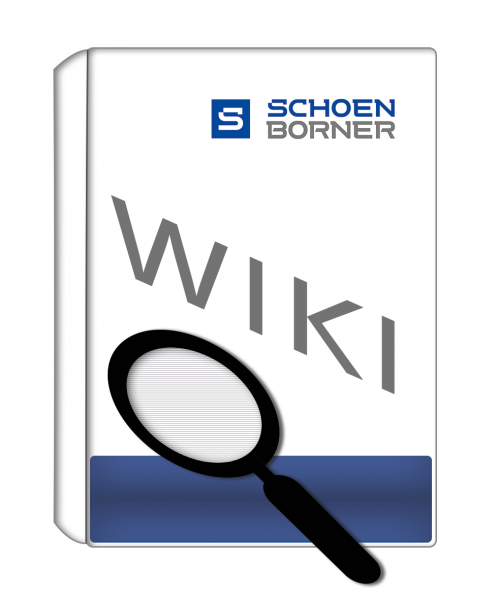
Wortbedeutungen:
- The component “cover cap” attached to the upper end of the EBG protective pipe system is the system termination of the protective pipe system and seals it against the penetration of function-influencing impurities.
- When using telescopic EBG, the collar of the cover cap serves as an installation length fixation. This is supported by the surrounding and compacted filling material of the EBG.
- The wiper cap is fixed to the upper end of the lower protective tube. It is made of TPE and has a sealing lip that rests against the telescopic protective tube. The wiper cap wipes off adhering impurities in the course of minimising the overall length (telescoping). This minimises the risk of impurities affecting the function of the EBG.
The plastic elements fixed to both rod partners have the task of preventing unintentional overstretching of the construction length.
The DVGW worksheet GW 336-2 (P) September 2010 states:
Anti-extension device for telescopic EBGs: “Telescopic EBGs must have an anti-extension device that can withstand a force of at least 150N.”
This is to prevent the unintentional destruction of the functionality of the EBG in the course of adjusting the overall length.
- The actuating square forms the upper end of the linkage system. The actuating key according to DIN 3223 is placed on the actuating square for torque transmission. The dimensional specifications are fixed in the technical test specification DVGW GW 336-2 (P)│September 2010.
Type of galvanisation for castings.
- It is impossible for individual parts of the protective tube system to be separated from each other unintentionally during the assembly of the coupling system.
This is ensured by a cable tie, which is located in the rod hole, in which the connecting means for the coupling assembly will later be fixed. Before mounting the coupling system, the linkage must be pulled out of the area of the protective tube bell. Only then may the cable tie (without tools) be loosened.
- includes all components that are connected to the linkage components:
Square steel and
square tube/square tubes. - Depending on the variant, this includes the coupling system.
- The plastic elements used for torque transmission as well as for brake and pull-out protection are exposed to great stress. The suitability of the plastic elements made of fibre-reinforced special plastic was examined in many test runs.
- Higher strength compared to mild steel S235JR.
Yield strength ≥ 350 MPa. Plastic deformation only occurs above 350 MPa.
Tensile strength ≥ 420 MPa (≤560 MPA). Material failure can only occur from 420 MPa. - The square tube was developed in collaboration with a European steel rolling mill to suit the task. Particular emphasis was placed on the design for torque transmission.
In order to ensure optimum functionality in telescoping, attention was paid to maintaining optimised manufacturing tolerances. This is matched to the square tube used and its function within the square tube pairing.
- In order to improve and secure the functionality of the protective pipe system, an internal, pivoting rod centring device is installed in the protective pipe bell.
Background: In the course of compacting filling material in the pipe trench, the filling material is compressed and moved in the lateral direction of materials that are not yet or less compacted. The forces acting laterally on the protective pipe system usually cause the protective pipe system to be pressed against the rod system over a large area, resulting in functional impairment. The internal, rotatably mounted boom centring minimises the effect of the force, because the contact point is reduced to a minimum and is also rotatably mounted.
- To actuate telescopic fittings laid in the ground, a manually applied force (torque) is transmitted to the actuating element “EBG” by means of an actuating key. To ensure that the torque is transmitted as gently as possible, a ball-bearing rod rotary union is installed in the system termination of the protective conduit system. The load is transmitted from the actuating square to the rod rotary union via stainless steel balls which are guided in a race made of fibre-reinforced plastic.
- To actuate adjustable and rigid valves laid in the ground, a manually applied force (torque) is transmitted to the actuating element “EBG” by means of an actuating key. Here, the load is applied from the actuating square via the rod rotary union to the rod.
- The cover cap attached to the upper end of the EBG’s protective tube system forms the system termination of the protective tube system.
- The actuating square is the upper termination of the boom system.
- A product configurator is a tool that supports the user in the design/combination of a product that can be assembled according to properties. This product is automatically assembled step by step according to corresponding properties and rules of constructability.
- In this way, the customer is given a personalised product experience, whereby he himself controls the process of creating a product that is individually adapted to his needs.
- The boom system consists of an upper and lower boom partner:
Square steel / Square tube
Square tube / Square tube - Spring-loaded plastic elements between the boom partners create a braking effect (self-locking). As the boom system and the protective tube system form one unit in the telescopic EBG, the braking effect has a restraining effect on the entire EBG in the course of the overall length adjustment.
Background: Using a vibrator or tamper, the filling material filled in the pipe trench is compacted/compressed. The vibrations generated in the process are transmitted to the EBG. If the braking force/self-locking is inadequately designed, the set construction length of the EBG changes unintentionally. To prevent this, a spring length adjusted to the EBG weight is used depending on the linkage cross-section and length.
- In the DVGW worksheet GW 336-2 (P) September 2010 it is written
Self-locking for telescopic EBG: “Telescopic EBGs must be telescopic in the specified boom length range and self-locking in any specified extension position”.
- The washing in of impurities that influence the function of the actuating element is minimised.
- The DVGW worksheet GW 336-2 (P) September 2010 states:
Upper closure of the sleeve pipe: “To protect against the ingress of contamination, the sleeve pipe must be provided with a suitable cover at the top.” - This function is performed by the cover cap.
- The DVGW worksheet mentioned above specifies the dimensions of the interface between the valve and the EBG. The protective pipe bell also complies with these specifications.
- includes all components that are inseparable from the protective tubes welded and plugged in.
- Depending on the variant, this includes
in the case of EBG for house connection gate valves, the rod rotary union and
in the case of EBG for network gate valves, the actuating square protector.
- The installation length of the installation extension spindles is continuously adjustable within the specified installation length range before installation. After installation or after mounting on the fitting, this value is reduced because the mounting position of the coupling element does not correspond to that of the protective tube bell. In order for the coupling element to reach the mounting position, it must be pulled out of the protective tube system by a certain amount. The adjustment range changes by this amount and, correspondingly, the minimum construction length range to be achieved.
- The height adjustment is infinitely variable, as there is no adjustment element with which the height can be adjusted.
When using telescopic EBG, the collar of the cover cap serves to fix the overall length/height adjustment. This is supported by the surrounding and compacted filling material of the EBG.
Protective pipe against coarse external backfill (gravel) in the ground for telescopic EBG’s.
- With the telescopic pipe system consisting of two PE pipes, the telescopability of the protective pipe system is realised. The dimensions of the protective pipes are selected in such a way that the gap between the two pipes does not negatively affect the telescoping capability of the EBG system, but ensures a certain degree of system stabilisation.
- The functional position of the protection tubes in the protection tube system has a decisive influence on the feasibility of a functional construction length adjustment. The telescopic protective tube must be guided in the lower protective tube for this purpose.
- is used for road vehicles in Germany (colloquially municipal orange). RAL colours are colours standardised by the RAL Institute.
- unalloyed structural steel
- Yield strength 185 – 355 MPa. Plastic deformation can occur from 185 MPa.
- Tensile strength 340 – 510 N/mm². Material failure can already occur from 340 MPa.
- Depending on the EBG model, the complete EBG consists of the system components:
Protective tube system - Linkage system
- coupling system.
- All systems are inseparable/separable from each other. The system concept behind this allows for variability in the structure of the entire system.
It is impossible for system components to become unintentionally detached during transport from the manufacturer to the purchaser and purchaser/supplier to the end customer.
Zinc flake coatings are coatings applied by the dip-spin process, consisting of a mixture of zinc and aluminium flakes bonded by an inorganic matrix. Supplemented by one or more layers of an organic or inorganic topcoat. The pre-treatment is carried out according to standard or customer specifications by blasting or phosphating. Very high corrosion protection values are achieved.
The danger of infiltration, which exists with lacquers, is prevented by the sacrificial effect of the zinc. Zinc flake coatings achieve better results in the salt spray test than a typical galvanic zinc coating, which often only achieve 96h to 200h in this test (usually according to DIN EN ISO 9227). On the other hand, they have a very good corrosion protection of 240h to 1500h.
Good chemical resistance
In addition to applications in the automotive industry, these coating systems are also found in wind turbines, the construction industry and automotive engineering.
Advantages:
- Very high corrosion protection for demanding applications.
- adjustable friction coefficients due to topcoats with integrated lubricants Resistant to organic solvents
- temperature resistance up to 180°C
- reduced contact corrosion between aluminium and stainless steel
- no hydrogen embrittlement even with high-strength components
- REACH compliant surface, chromium(VI)-fre
Schönborner – Newsletter
Immer gut informiert auf dem neuesten Stand: Erfahren Sie als erster von innovativen Produkten und exklusiven Aktionen. Melden Sie sich zu unserem Newsletter an!